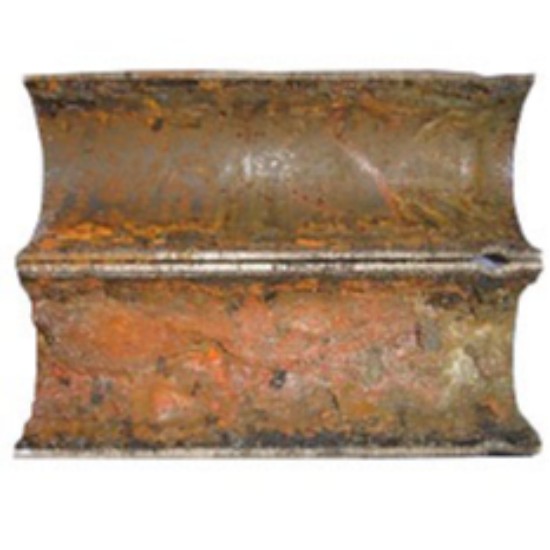
Microbiologically influenced corrosion (MIC) was once thought to be the primary threat to sprinkler pipe longevity. However, further research has found that oxygen is the primary factory in sprinkler pipe corrosion for both wet and dry pipe systems. In this article, we will discuss how corrosion occurs in a dry sprinkler system and the options for preventing or slowing this corrosion in order to maintain your system and extend the life of your sprinkler piping.
The corrosion triangle illustrates the three factors necessary for corrosion to take place: an unprotected metal, electrochemical potential in the form of oxygen, and electrolyte in the form of moisture. When all three factors are present, there interaction results in corrosion of the unprotected metal. To prevent corrosion, you must remove one factor in the corrosion triangle.
Removing the Unprotected Metal from the Equation
Galvanized steel prevents corrosion by having a protective surface between the metal and the water or air; Black steel pipe has little to no protective coating. However, both galvanized steel and black steel pipes present opportunities for corrosion – an issue we will go into further in a future blog.
Removing Water from the Equation
The definition of a dry sprinkler pipe system says that the sprinkler pipes are dry – without water. And this is true, the purpose of a dry sprinkler system is to provide piping without water in sensitive areas, such as areas where the water in sprinkler pipes would freeze or locations where any water leakage could cause serious damage. (Although, if your sprinkler system is located in an area where any water can cause serious damage to the facility or equipment, it is best to look at other fire suppression options such as aerosol based or clean agents.)
However, dry sprinkler pipes will still collect trace amounts of water due to hydrotesting, flow testing, and condensation. Even when you properly drain the system on a regular basis (read more on how to drain your dry system pipes here - drip drum blog), the water is present and can react with the pipe and oxygen to create corrosion. The remaining option is to remove the oxygen from the dry pipe system in order to prevent corrosion.
Removing Oxygen from the Equation
Dry sprinkler and pre-action system pipes are pressurized with air until the system is alerted that a fire is occurring, at which time the sprinklers activate releasing the air from the system and filling the pipes with water. Instead of pressurizing these pipes with air, however, you can pressurize them with nitrogen, which does not react with the water or pipes to create corrosion.
Ongoing, long-term exposure tests have been conducted, and have shown that nitrogen filled sprinkler pipes slow or stop corrosion and extend the life of the sprinkler pipes significantly. This preventative measure for your dry sprinkler system can save you money in costly repairs due to corrosion including property and equipment damage, ongoing repairs to pipes or full system replacement, sprinkler head blockages, and an inoperable fire protection system that puts your people and assets at risk.
Nitrogen arrests electrochemical, galvanic and MIC corrosion. The nitrogen also prevents ice plugs by ensuring a -40F to -70F dew point within the sprinkler system. As high purity nitrogen enters the sprinkler piping, corrosive oxygen is displaced – preventing corrosion, slowing corrosion that may already have occurred, and maintaining your sprinkler system for a longer life span.