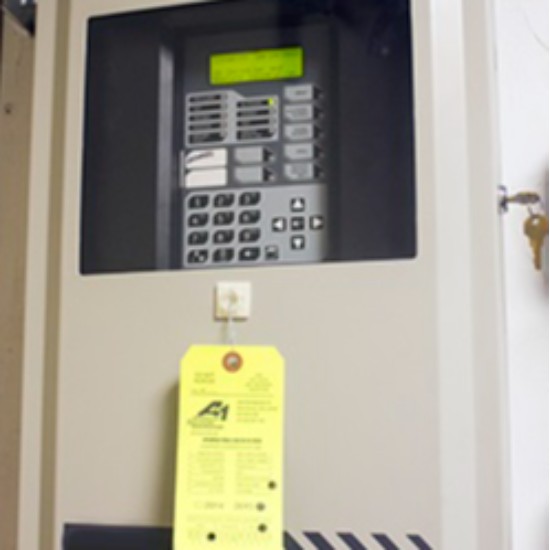
Limit the inconvenience of trouble signals from your Fire Alarm system by being pro-active in replacing batteries.
Fire alarms are a system of multiple devices working together to detect and warn people through visual and audio appliances when smoke, fire, carbon monoxide or other emergencies are present. The fire alarm panel is the electrical panel that monitors all components of the system. It also sends trouble signals for problems found within the fire alarm system, problems which may cause the system to not work properly and put your people and assets at risk. Fire alarm systems are prone to errors given the sheer number of devices involved so regular inspections and maintenance are key in keeping your system operating properly. Regular maintenance can also limit the number of trouble signals you receive each year as your Life Safety Partner will inspect and service the devices to keep them running properly.
Fire alarms need to be able to work during an emergency, and since emergencies can cause power outages a battery back-up to your system is an important component. When your battery power runs low, your fire alarm system will send a trouble signal to the central monitoring station, who will then call the system owner. The fire alarm panel will also beep locally at the panel and annunciator if one is present.
Trouble signals from your Fire Alarm system won’t wait for a convenient time; whether you are in a meeting, out of town, or sleeping at 2 a.m. you will be receiving the alert and need to address it immediately. By pro-actively replacing your system batteries every two years, you can limit both the number of trouble signals you receive and the increased costs of emergency service from your Life Safety Partner.
Parts of the Fire Alarm System:
Fire alarm control panel (FACP) – also known as the fire alarm control unit, is the hub of the system. It monitors inputs and system integrity, controls outputs and relays information.
Smoke Detectors – smoke detectors have built in sensors, and when smoke is found in the atmosphere, they send information to the fire alarm panel. The two most common types of smoke detectors are ionization and photoelectric. The sensing chambers of these detectors operate differently to sense visible or invisible combustion particles from developing fires.
Primary power supply – commonly the non-switched 120 or 240 volt alternating current course supplied from a commercial power utility. In non-residential applications, a branch circuit is dedicated to the fire alarm system and its constituents. “Dedicated branch circuits” should not be confused with “Individual branch circuits” which supply energy to a single appliance.
Secondary (backup) power supplies – This component, commonly consisting of sealed lead-acid storage batteries or other emergency sources including generators, is used to supply energy in the event of a primary power failure.
Initiating devices: This component acts as an input to the fire alarm control unit and are either manually or automatically activated, such as pull stations, heat detectors, or smoke detectors. Heat and smoke detectors have different categories of both kinds. Some categories are beam, photoelectrical, aspiration, and duct.
Notification appliances: This component uses energy supplied from the fire alarm system or other stored energy source, to inform people of the need to take action, usually to evacuate. This is done by means of a flashing light, strobe light, electromechanical horn, “beeper horn”, chime, bell, speaker, or a combination of these devices.
Building safety interfaces: This interface allows the fire alarm system to control aspects of the building environment and to prepare the building for fire, and to control the spread of smoke fumes and fire by influencing air movement, lighting, process control, human transport and exit. Building safety interfaces include magnetic smoke door holders, duct mounted smoke detection, emergency elevator service, and public address rack.
Can you ensure each device in your fire alarm is being inspected and tested? You can if your Life Safety Partner uses a barcoded method of inspection, ensuring the inspector finds and tests each device efficiently. Your inspection report should list the results for each device, as well as the date/time stamp for when it was last inspected. These details will provide you with piece of mind and your AHJ inspector with full system information.
A1 is a leading expert on the latest technology in life safety. To find out more information or to ask a question, click here or call us at 1-800-859-6198.