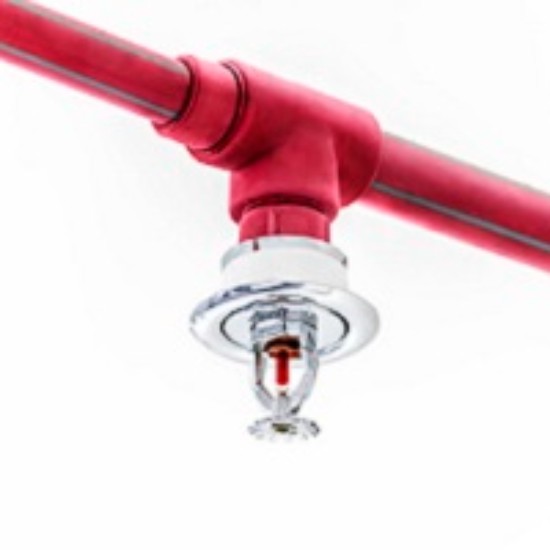
Fire sprinkler systems experience corrosion due to the interaction of oxygen, an unprotected metal, and moisture. In 25 years, 35% of wet fire sprinkler systems have significant corrosion issues. In only 12.5 years, 73% of dry and pre-action systems have significant corrosion issues.
Corrosion will cause leaks in your sprinkler pipes, resulting in costly repairs which may include replacing piping, fittings, or even the entire system, facility or equipment damage from water leaks, and sprinkler head blockages.
To combat corrosion, fire sprinkler systems utilize either galvanized steel or black steel for pipes, as each type of steel has corrosion resistant properties.
Galvanized and Black Steel
Galvanized steel pipe is hot-dipped in zinc to have a protective coating on the walls of the pipe. The zinc coating, or galvanizing, acts as a sacrificial anode to reduce the corrosion of steel pipe. However, galvanized steel pipe does corrode in any pitted area or space where the galvanized coating is damaged or missing.
Black steel pipe has little to no protective coating. This is the most commonly used steel pipe for sprinkler systems. The oxygen within the water is quickly dissipated, thus reducing the corrosion potential. However, black steel pipe does corrode in a uniform thinning of the walls.
Corrosion Solution
Since neither type of steel is able to stop corrosion, one of the other agents in corrosion, either oxygen or moisture, must be addressed in order to stop the problem. While water is inevitable in sprinkler pipes (even dry system pipes will have condensation), Oxygen can be replaced with Nitrogen – effectively breaking the corrosion triangle.
Dry and Pre-Action systems can be pressurized with Nitrogen, instead of air. Wet systems can have the pipes charged with Nitrogen before being flushed with water, so that any “air” pockets are actually pockets of Nitrogen. Read more about corrosion solutions specifically for Dry/Pre-Action Systems and Wet Systems.
Testing Corrosion Rates in Steel Pipes
An independent lab has been conducting ongoing, long-term exposure tests to compare the performance of Nitrogen vs Oxygen, in both black steel (schedule 10) and galvanized pipe, and the effects on corrosion. Each pipe segment is subjected to compressed air or supervisory nitrogen, as they would be in a practical application of a dry pipe fire sprinkler. At regular intervals, the pipes are opened and the amount of corrosion is measured so that the rate of corrosion can be calculated.
The images below show pipe segments that have been exposed to either compressed air or 98% Nitrogen for 6.5 years, and in both the state the pipe was received and then that pipe segment cleaned. At the rate of corrosion found, the Black Steel Pipes would last 19.8 years with compressed air and 60.9 years with 98% Nitrogen. The Galvanized Steel Pipes would last 9.2 years with compressed air and 162.3 years with 98% Nitrogen. The results clearly show that a significant cost savings can be realized by using black steel pipe in combination with Nitrogen supervision.
Black Steel
Black Steel, filled with compressed air
Black Steel, filled with 98% Nitrogen
Galvanized Steel
Galvanized Steel, filled with compressed air
Galvanized Steel, filled with 98% Nitrogen
A1 is a leading expert on the latest technology in life safety. To find out more information or to ask a question, click here or call us at 1-800-859-6198.